摘 要
水性聚氨酯涂料是以水代替有机溶剂作为分散介质的新型聚氨酯体系,将乳液稀释,原料水除了用作聚氨酯的溶剂或分散介质,水还是重要的反应性原料,在聚氨酯预聚体分散于水的同时,水也参与扩链。水性聚氨酯是具有高强度、撕裂、耐磨等特性的高分子材料。
由于聚氨酯合成反应放热量比较大,控制不当易凝胶,对于反应设备的要求是传热快,易清洗,此外聚氨酯反应为逐步聚合反应的特点,造成反应过程中加料是分批加入的,第一步的加料量一般为总量的30﹪,所以对反应设备的要求是长径比大于1:1,大的可以到2:1,长径比大时,物料与釜体接触面积大,有利于设备传热。对于分散设备的要求是快速,剪切力大,可以调速。
本文着重分析了丙酮法合成水性聚氨酯涂料工艺过程,结合自身工作岗位分析了水性聚氨酯的原料、设备及丙酮法操作,对水性聚氨酯涂料所存在的问题进行了总结并提出了工艺改进措施。
关键词:水性聚氨酯,高分子材料,丙酮法,设备,原料
1 前言
1.1 水性聚氨酯涂料的发展现状
水性涂料是以水作溶剂或分散介质的涂料。最早的商品化水性涂料是在20世纪30年代出现的。基于其对环境的相容性和保护性,并具有节省资源、节约能源的优点,水性涂料产品很快就被市场接受,并逐渐发展扩大。日本、美国1986年水性涂料分别占涂料总销售量的18%和22%,英国1995年水性涂料产量占全国涂料总产量的64.5%。我国从60年代开始研究水性涂料,进入90年代后,国家大力扶持水性涂料的发展。目前的市场占有率不高,但是发展前景很好。
聚氨酯是氨基甲酸酯树脂的简称,其分子中含有特征单元结构氨基甲酸酯(-NH-CO-)。聚氨酯应用十分广泛,作为涂料具有良好的耐磨性、耐腐蚀性、耐化学品性、硬度大、高弹性等优点。水性聚氨酯(PU)是水性涂料中很有发展潜力的一种,在很多领域都得到了广泛的应用,它包括单组分聚氨酯涂料和双组分聚氨酯涂料两种,是以水为介质的二元胶态体系,不仅具有无毒、不易燃烧、不污染环境、节能、安全可靠、不易损伤被涂饰表面、易操作和改性等优点;同时还具有溶剂型聚氨酯的一些重要的性能特征,使得它在织物、皮革涂饰及粘合剂等许多领域得到了广泛的应用。
单组分水乳型聚氨酯的特征在于很高的断裂伸长率(达到800%以上)和较高的抗拉伸强度(达20MPa左右),但因其具有线型结构,分子中含有亲水基团,其耐水性、耐溶剂性较差,应用受到了限制。
水性双组分聚氨酯涂料的应用领域基本上与溶剂型涂料相当,既可用于热敏材料(如木材、塑料)和不能烘烤的大型物件,也可用于诸如汽车类的烘烤物件.通过对报道的实验数据进行对比,表明,水性双组分聚氨酯涂料除了干燥时间稍长和适用期稍短外,涂膜的装饰性、机械性能、耐化学性和耐候性均可与溶剂型双组分PUD涂料相媲美。
1.2水性聚氨酯涂料用途及优缺点
1.2.1水性聚氨酯涂料用途
随着经济发展和人们生活水平提高,各国对挥发性有机物及有毒物的限制越来越严格,20世纪90年代,国际上兴起“绿色革命”,促进全球工业向“绿色”方向迈进。PUD的低VOC含量,符合发展绿色工业的“三前提”(资源、能源、无污染)及“四E原则”(经济ECONOMY、效率EFFICIENCY、生态ECOLOGY、活力ENERGY)。虽然聚氨酯具有天然的优良机械性能。然而水性聚氨酯在环保方面比它更有优势,而且随着人们对水性聚氨酯的研究,目前水性聚氨酯分散体已在通用溶剂型聚氨酯所覆盖的领域大量使用,成功地应用于轻纺、皮革加工、涂料、木材加工、建材、造纸和胶粘剂等行业。聚氨酯乳液涂饰后的皮革,具有光泽度高、手感好、耐磨耗、小易断裂、弹性好、耐低温性能和耐挠屈性能优良等特点。此外,在纺织品涂层整理中有广泛的应用。水性聚氨酯对纺织品的成膜性好、粘接强度高、能赋予织物柔软、丰满的手感,改善织物耐磨性、抗皱性、回弹性、通透性和耐热性等。
水性PU比有机溶剂型PU应用成本低、无公害、易处理、粘合效果好,在胶粘剂及涂料行业有很好的发展前景。聚氨酯离子聚合物对天然和合成橡胶表面均具有很好粘接性,应用于鞋类的制造。目前,水性聚氨酯主要用作家具漆、电泳漆、电沉积涂料、建筑涂料、纸张处理涂料、玻璃纤维涂料等。除此之外水性涂料还有一些特殊用途,如用作安全玻璃的中间涂膜,以制成不碎裂的安全玻璃,广泛用于汽车、飞机、轮船或航天仪器。水性分散体主要用作金属涂料,如阳离子型电沉积涂料被广泛用于汽车底漆,以提高车体的抗腐蚀性能。水性PU在纺织和印染助剂方面的应用越来越广泛。如用作染色助剂、涂料印花粘接剂、柔软与防皱整理剂、抗静电和亲水整理剂等,可提高其染色深度、牢度以及纺织物的其他性能。近年来,水性PU也广泛用于石油破乳剂,造价低、破乳效果好、速度快、无毒、使用方便。此外,在聚氨酯主链上接枝多氟烷基,即可制作优良的防水、防油、防污剂;在其主链上接枝卤素、磷等元素,也可制成优良的阻燃整理剂等。水性聚氨酯开始被越来越广泛的使用。
1.2.2水性与溶剂型聚氨酯涂料比具有的优缺点
水性聚氨酯是以水为介质的二元胶态体系,聚氨酯粒子分散于连续的水相中,有人也称水系聚氨酯或水基聚氨酯。与溶剂型聚氨酯比,水性聚氨酯除了无溶剂臭味、无污染等优点,具体如下表:
表1.1 水性与溶剂型聚氨酯涂料的性能比较
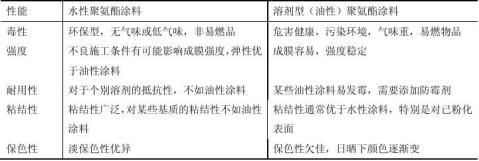
1.3水性聚氨酯的合成方法
水性聚氨酯的制备通常采用两类方法:外乳化法和自乳化法。外乳化法将聚氨酯预聚物缓慢加入到含乳化剂的水中,形成粗粒乳液,再送入乳化器形成粒径适当的乳液。该法制备的聚氨酯乳液胶体稳定性较差,适于材料的表面处理,如羊毛的不粘处理等。水性聚氨酯乳液的制备多采用聚合物自乳化法,即在聚合物分子链上引入适量的亲水性基团,在一定条件下分散形成稳定乳液。自乳化法操作简单,制得的乳液性能比外乳化法要好,目前合成水性聚氨酯都采用这种方法。
自乳化法分为:丙酮法、预聚体法、熔融分散法、酮亚胺-酮连氮法、保护端基乳化法。
1.3.1丙酮法
首先合成含-NCO端基的高粘度聚氨酯预聚体,再以有机溶剂稀释预聚体,然后再进行乳化的方法。在溶剂存在下,预聚体与亲水性扩链剂进行扩链反应,生成较高分子量的聚氨酯,反应过程可根据所需要加入溶剂以降低聚氨酯溶液黏度,使之易于搅拌,然后加水进行分散,形成乳液,最后蒸去溶剂。溶剂以丙酮,故称为丙酮法。
特点:易于操作,重复性好,制得的水性聚氨酯分子量可变范围宽粒粒径的大小可控,产品质量好,是目前生产水性聚氨酯的主要方法。但该法需要耗费大量低沸点丙酮,易造成环境污染,工艺复杂,成本高。
1.3.2预聚体法
预聚体法是近年来发展起来的,它是将水性单体引入到预聚物链中,制成亲水性的聚合物链,得到亲水改性的端—NCO基聚氨酯预聚体,由于预聚体的分子量不是太高,粘度不大,可不加溶剂稀释,或仅需在水中以少量溶剂稀释就能在剪切力作用下分散于水中,再用亲水性单体(二胺或三胺)将其部分扩链,生成相对分子量高的水性聚氨酯,最终得到水性聚氨酯分散液。为合成低粘度预聚体,通常选择脂肪族或脂环族多异氰酸酯,因为这两种多异氰酸酯反应活性低,预聚体分散于水中后用二胺扩链时受水的影响小。但分散过程必须在低温下进行,以降低—NCO与水反应活性;须严格控制预聚体粘度,否则预聚体在水中分散将非常困难。
特点:此法避免了有机溶剂的大量使用,工艺简单,便于工业化连续生产。缺点是扩链反应在多相体系中发生,反应不能按定量的方式进行。
1.3.3融熔分散法 熔融分散缩聚法又称熔体分散法,是一种制备水性聚氨酯的无溶剂分散法。该法把异氰酸酯的加聚反应和氨基的缩聚反应紧密地结合起来。先合成带有亲水性离子基团和端-NCO基的聚氨酯聚合物,预聚物与尿素进行加聚反应得到含离子基团的端脲基聚氨酯低聚物。此低聚物在熔融状态下与甲醛水溶液发生缩聚反应和羟甲基化反应,形成含羟甲基的聚氨酯双缩二脲,用水稀释后,得到稳定的水性聚氨酯分散液。 特点:反应过程不需要溶剂,工艺简单,易于控制,配方可变性较大,不需要特殊设备,因此具有广阔的发展前景。但反应温度高,生产水性聚氨酯分散体为支链结构,分子量较低。
1.3.4酮亚胺-酮连氮
亚胺-酮连氮法是指封闭二胺和封闭联胺被用作潜在的扩链剂加到亲水性—NCO官能封端预聚物中,二胺和联胺与酮类反应分别得到酮亚胺和酮连氮。当水分散该混合物时,由于酮亚胺的水解速度比—NCO与水的反应速度快,释放出二元胺或肼与分散的聚合物微粒
反应,得到的水性聚氨酯-脲具有良好的性能。
酮亚胺/酮连氮法适用于由芳香族异氰酸酯制备水性聚氨酯分散液,该法融合了丙酮法、预聚体混合法的优点,是制备高质量水性聚氨酯的重要方法。
1.3.5保护端基乳化法
使用酚类、甲乙酮亚胺、吡咯烷酮、亚硫酸氢钠等封闭剂,将带有亲水性离子基团和-NCO封端的聚氨酯预聚物的端-NCO基团保护起来,使-NCO基团失去活性,制成一种封闭式的聚氨酯预聚体,加人扩链剂和交联剂共同乳化后,制成水性聚氨酯分散液。应用时,加热可使预聚物端-NCO基团解封,-NCO基团与扩链剂、交联剂反应,形成网络结构的聚氨酯胶膜。
特点:此法对工艺要求颇高,乳液稳定性差,关键在于选择解封温度低的高效封闭剂。
2 水性聚氨酯涂料生产
我所在的生产车间主要用丙酮法生产聚氨酯产品,用多元醇和异氰酸酯经催化剂聚合反应之后,加入大量丙酮稀释,再加扩链剂扩链,后加水经强剪切力作用下分散,生成成品粗乳液,其中粗乳液中含有溶剂水和溶剂丙酮,需要将乳液中的水和丙酮分离出来才能够生产出合格的成品乳液,并且乳液固体含量需要达到50.0%±0.5%。
2.1原料介绍
制备水性聚氨酯的原料大致相同,其应用方向的改变多由原料的不同配比和不同的催化剂而决定,因为物料量和催化剂的理化性质属于保密范畴,所以对物料量及催化剂理化性质不多做介绍。生产所用基本原料如下表:
表2.1 生产用基本原料表
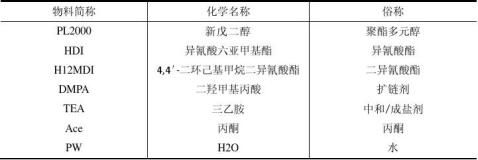
2.1.1聚酯多元醇
聚酯多元醇,有机物,通常是由有机二元羧酸(酸酐或酯)与多元醇(包括二醇)缩合(或酯交换)或由内酯与多元醇聚合而成,常温下是固体。二元酸有苯二甲酸或苯二甲酸酐或其酯、己二酸、卤代苯二甲酸等。多元醇有乙二醇、丙二醇、一缩二乙二醇、三羟甲基丙烷、季戊四醇等。不同品种的聚酯多元醇由于种类不同或制备工艺不一样,性质也不一样,对于聚酯多元醇比较重要的几个指标是羟值、酸值、水分、粘度、分子量、密度以及色度等。聚酯多元醇的特性及用途:聚酯型聚氨酯因分子内含有较多的酯基、氨基等极性基团,内聚强度和附着力强,具有较高的强度、耐磨性。涂料用聚酯树脂(分子量2000-5000)主要以新戊二醇和间、对苯二甲酸等
2.1.2异氰酸酯
制备聚氨酯乳液常用的二异氰酸酯有甲苯二异氰酸酯(TDI),4,4-二苯基甲烷二异氰酸酯(MDI)等芳香族二异氰酸酯,以及异佛尔酮二异氰酸酯(IPDI),六亚甲基二异氰酸酯(HDI),4,4-二环己基甲烷二异氰酸酯(H12MDI), 1,12-十二烷基二异氰酸酯(C12DDI)等脂肪族、脂环族二异氰酸酯。
由于脂肪族或脂环族二异氰酸酯制成的聚氨酯,耐水解性比芳香族二异氰酸酯制成的
聚氨酯好,水性聚氨酯产品的贮存稳定性好,另外脂肪族二异氰酸酯耐黄变性比芳香族二异氰酸酯好得多,所以国外高品质的聚酯型水性聚氨酯一般均采用脂肪族或脂环族二异氰酸酯制成。
我所在的水性聚氨酯车间所用的则是HDI和H12MDI:
表2.2 HDI与H12MDI的物化性质

六亚甲基二异氰酸酯(HDI)
NCOCH2NCO
二环己烷基甲烷二异氰酸酯 (H12MDI)
2.1.3扩链剂DMPA
分子式:C5H10O4 分子量:134.03
物化性能:白色结晶粉末,熔点175-185℃,溶于丙酮、甲醇,不溶于苯、甲苯。新戊基结构使它有良好的耐热性、耐水性和颜色稳定性,带有羧基的二元醇结构又赋予它一些特殊用途。
产品用途:DMPA是一种多用途的有机原料。本产品在水性聚氨酯制造中既是扩链剂,又能使聚氨酯获得自乳化性能,可制成稳定性优良的自乳化性水性聚氨酯;还用于制备聚氨酯水乳液型皮革涂饰剂,是传统的水乳性聚丙烯酸酯皮革涂饰剂的升级换代产品
2.1.4三乙胺(中和剂/成盐剂)
三乙胺,有机化合物,是具有有强烈的氨臭的淡黄色透明液体,在空气中微发烟。微溶于水,可溶于乙醇、乙醚。有碱性,与无机酸生成可溶的盐类。 2.1.5溶剂(丙酮或甲乙酮)
在聚氨酯乳液制备中,为了降低粘度,利于预聚体的分散,可加入适量有机溶剂,可采用的有丙酮、丁酮、甲乙酮、二氧六环、N,N一二甲基酰胺、N一甲基毗咯烷酮等水溶性(或亲水性)有机溶剂和甲苯等憎水性溶剂。考虑到成本、操作性等因素,最常用的是丙酮,一下是丙酮的相关理化性质:
表2.2 丙酮的理化性质
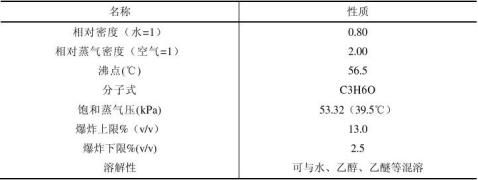
2.1.6水
所谓水性聚氨酯即是以水代替有机溶剂,将乳液稀释,原料水除了用作聚氨酯的溶剂或分散介质,水还是重要的反应性原料,合成水性聚氨酯目前以预聚体混合法为主,在聚氨酯预聚体分散于水的同时,水也参与扩链。所以对所使用的原料水必须是严格控制的,其中重要的控制指标是水的温度、电导率及PH值等,其中水中的钙、镁离子对乳液的稳定性能影响最大,平时化学试剂工艺水即可满足生产需求。
2.2工艺原理流程简图及方框图
我在的车间生产主要是多元醇和异氰酸酯经催化剂聚合反应之后,加入大量丙酮稀释,再加扩链剂扩链,后加水经强剪切力作用下分散,生成成品粗乳液,在将乳液中的水和丙酮分离出来生产出合格的成品乳液。主要反应方程式:
R?NCO+R′?OH→RNHCOOR′
主要分为投料、预聚反应、中和扩链、分散、脱溶剂(脱丙酮)五大部分。
图2.1 基本工艺流程图
图2.2 基本工艺流程方框图

2.3工艺流程讲解
2.3.1投料
公用工程准备好,夹套冷冻水循环起来(给多元醇降温)。把生产某种产品的聚酯多元醇(一般加热到100度左右)加入预聚釜中,加入到能钩到搅拌的量时启动搅拌。然后加入小分子多元醇。加入其它散称物料,如DMPA。适宜温度下加入多异氰酸酯。如HDI、HMDI然后少量丙酮稀释。适宜温度下加入催化剂。
2.3.2 预聚反应
加入催化剂后,等待反应自然升温,然后多次小量蒸汽加热,直至目标温度。温度要控制在反应温度,不能超过反应温度,否则副反应会增加,影响产品性能。然后取样分析-NCO﹪。-NCO﹪合格后,降温,加入大量丙酮稀释(丙酮会影响分散后乳液的粒径和黏度,所以加入丙酮量要准)。转至扩链釜。其中主要反应为异氰酸酯与聚酯多元醇的反应,反应方程式:
R?NCO+R′?OH→RNHCOOR′
2.3.3 中和扩链
预聚体转至扩链釜后,启动搅拌,适宜温度下加入中和剂或扩链剂。中和的作用是与预聚体中羧基反应,中和成盐,是预聚体更具有亲水性。有些预聚体的分子链不符合要求,就要加入扩链剂进行扩链(链增长反应),使之在分散后粒径符合要求。反应一段时间后,准备转至分散釜。此阶段一定要注意扩链时间,扩链时间太长会出现扩链过度,导致分散后粒径过大。转至分散釜。
2.4.4 分散
转到分散釜后,开始加水分散,控制搅拌转速和加水的流量。分散就是把预聚体由油包水(水是亲水基团)的状态,然后亲水基团吸水,通过相转变(在相转变的这个节点,如果突然中断加水,会出现凝胶),形成水包油的现象。分散开后,继续搅拌一段时间,准备转至脱丙酮釜。注意加水流量和时间的控制,加水过快可能导致分散不均匀;加水过慢可能出现凝胶。
2.4.5 脱丙酮
分散好的粗乳液转至脱丙酮釜后,启动搅拌,加入消泡剂(防止脱丙酮过程起沫严重),然后开始启动真空机组,然后逐步提真空,直至全真空。每隔一小时取样测粒径,并观察釜内状况,是否起沫,如起沫严重,就要补加消泡剂。根据丙酮储罐的丙酮量和加入的丙酮量比较,再由理论固含计算,来估计脱丙酮结束时间,然后取样测固体含量。合格后,停真空。然后加入其它助剂和杀菌剂,并根据固含(一般高于理论值)补加工艺水。搅拌一段时间,开始包装。此阶段主要是对真空度的控制,在逐渐提高系统真空度来降低丙酮的沸点,从而更有利于脱除。注意在逐渐提高系统真空度的时候要注意脱丙酮反应釜内的乳液状态,防止乳液起沫过于严重,从而影响脱丙酮的效率。
3 生产所需设备
3.1预聚釜
水性聚氨酯的反应器一般为立式反应釜,带搅拌装置的罐式立式反应釜是间歇法合成聚氨酯乳液时应用最广泛的。我所在的岗位是容积3立方米的反应釜,主要由罐体、夹套、传动装置、轴封装置、螺带和框式复合式搅拌、进、出料口、容器法兰以及支座等构成,由蒸汽加热,冷冻水降温。
要指出的是,反应釜容积的加大能降低投资和操作费用,并能提高劳动生产率。例如,装置一台容积大一倍的反应釜比装置两台同容积的反应釜可降低投资20%-30%,并显著减少操作费用,还可以使产品稳定性提高。
但对于水性聚氨酯的制备,反应器容积增大会带来另一个问题,在反应物料体积增大时,反应器容积与物料体积放大倍数的立方成正比,而夹套的面积与放大倍数的平方近似成正比,即用于热交换的面积变化跟不上反应器容积的变化。而且预聚反应是很复杂的反应,往往温度高会带来更多的副反应,所以为了加大换热面积,只会把预聚釜做长,但由于装置限制,也不能做的太长。
表3.1 反应器容积与热交换比表面积变化的比较
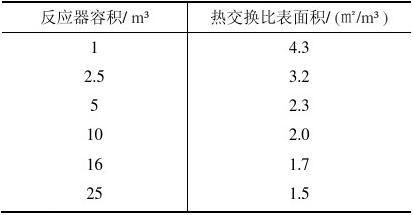
有些预聚釜为了更好的换热,采用夹套加热,内盘管降温两套控温系统,更利于控制温度变化。 3.2中和扩链釜
聚合完的预聚体是在中和扩链釜完成中和与扩链反应。主要由罐体、夹套、传动装置、轴封装置、螺带和框式复合式搅拌、进、出料口、容器法兰以及支座等构成。
加热方式与预聚釜不同,用热水加热,由冷冻水降温。 3.3分散釜
聚氨酯的乳化是在分散釜中完成的,油溶性的聚氨酯树脂即便是引入了亲水基团,它在水中的溶解也不是轻易实现的,必须借助剧烈搅拌等外力才能够完成。在水性聚氨酯乳液的生产过程中,对所选乳化设备的主要要求是:1,搅拌速度快,即能给树脂以强剪切力,以便使聚氨酯树脂均匀地分散在水中;2,转速可调,,以便乳化过程中进行必要的反
应。
分散釜与预聚釜、中和扩链釜主要的区别在于:分散釜不是夹套,是半盘管;搅拌是带锯齿的分散盘,为分散提供强剪切力;釜壁带有折流板,使混合效果更佳。 3.4脱溶剂釜
给脱丙酮提供足够的空间,搅拌是反向双搅拌,大搅拌为框式搅拌,小搅拌为平叶推进式搅拌,带有夹套。 3.5精馏塔
我所在的岗位精馏塔是填料塔,2.5米左右,我们主要目的是脱除丙酮,不需要给丙酮精馏。使用回流的方法,为塔顶和塔底有5-7℃的温度差提空场所,更容易的脱除丙酮。 3.6塔顶冷凝器
是一个列管式换热器,满足在蒸馏过程中对蒸发丙酮气冷凝的能力,防止丙酮气排放至大气中去,污染大气。 3.7真空泵
在实际生产过程中,需要考虑的因素有乳液的温度不得超过50℃,并且丙酮的沸点在常压下为56.5℃,所以在常压下将丙酮加热分离出来务必会严重影响产品的质量。所以要在负压条件下加热,将丙酮与PU乳液分离出来,并达到固体含量值在要求范围之内。
真空度最高可达到-0.1Mpa即可,并且在0至-0.1Mpa范围内可调压力,水环真空泵即可满足要求
4 总结
4.1水性涂料的发展趋势
随着科技进步和国民经济的高速发展,人们的环保意识日趋增强、对健康的要求越来越高,环保法规也日趋完善,节资节能,保护环境,已成为全球涂料界面临的主要问题。水性漆的开发在世界范围内受到重视:在欧美发达国家,水性漆的普及率已达80%以上。涂料工业大致可分为三个应用领域,而水性涂料在最大的两个应用领域中占有相当的比例。在建筑涂料领域里,水性涂料在工业发达国家中占绝对优势,比如在德国占到93%,即使在西欧发展最慢的挪威也有60%份额。在工业涂料领域里,欧洲的水性工业涂料已超过100万吨,2015年将达到200万吨。水性工业涂料在世界工业涂料中已占30%,到2015年将达到50%以上。现在欧洲水性工业涂料已占到40%;在专用涂料领域,目前水性涂料正在以前所未有的速度向汽车修补涂料、防腐蚀涂料、道路标示涂料等所占比重较大的领域发展。
4.2水性聚氨酯涂料的发展前景
目前,国内外生产的水性聚氨酯涂料几乎都是单组分的,而单组分体系的抗拉伸强度提高的程度很有限,对于高强度的涂膜,必须采用双组分体系,其综合性能与传统的溶剂型双组分聚氨酯产品相当,这正是当前国内外的发展方向之一。
由于溶剂型聚氨酯涂料对于人类自身和生态环境的严重威胁日益明显,绿色涂料替代溶剂型涂料成为必然。而水性聚氨酯涂料具有经济节能环保和安全的特点,符合时代发展的要求,势必得到大力的推广和应用。绿色涂料的开发和推广成为21世纪涂料的主要方向。聚氨酯涂料在我国的推广和应用取得了可喜的成绩,但是也存在一些空白,这都是有待提高的空间。相信随着市场的发展和中国科研力量的不断加强以及科研队伍的壮大,新的适合消费者需求的具有更高质量的聚氨酯涂料会不断得到开发和推广应用。